Warehouse mapping involves creating a detailed blueprint of storage locations and workflows within a warehouse. This process is essential for businesses aiming to optimize warehouse space, enhance inventory accuracy, and improve operational efficiency. Well-mapped warehouses facilitate faster order fulfillment, reduce labor costs, and streamline daily operations. This article will delve into the importance of warehouse mapping, key elements of a successful system, and practical steps to design an efficient warehouse layout.
Key Takeaways
- Warehouse mapping is essential for optimizing layouts, enhancing inventory management, and maintaining operational efficiency, which leads to improved compliance and competitiveness.
- A successful mapping system requires a structured approach, incorporating visual tools and regular updates to adapt to changes in inventory and operations, while engaging warehouse staff for their insights.
- Leveraging technology, such as integrating mapping with Warehouse Management System (WMS) and utilizing real-time monitoring, can significantly improve inventory tracking and optimize workflows, addressing common challenges.
The Importance of Warehouse Mapping for Operational Efficiency
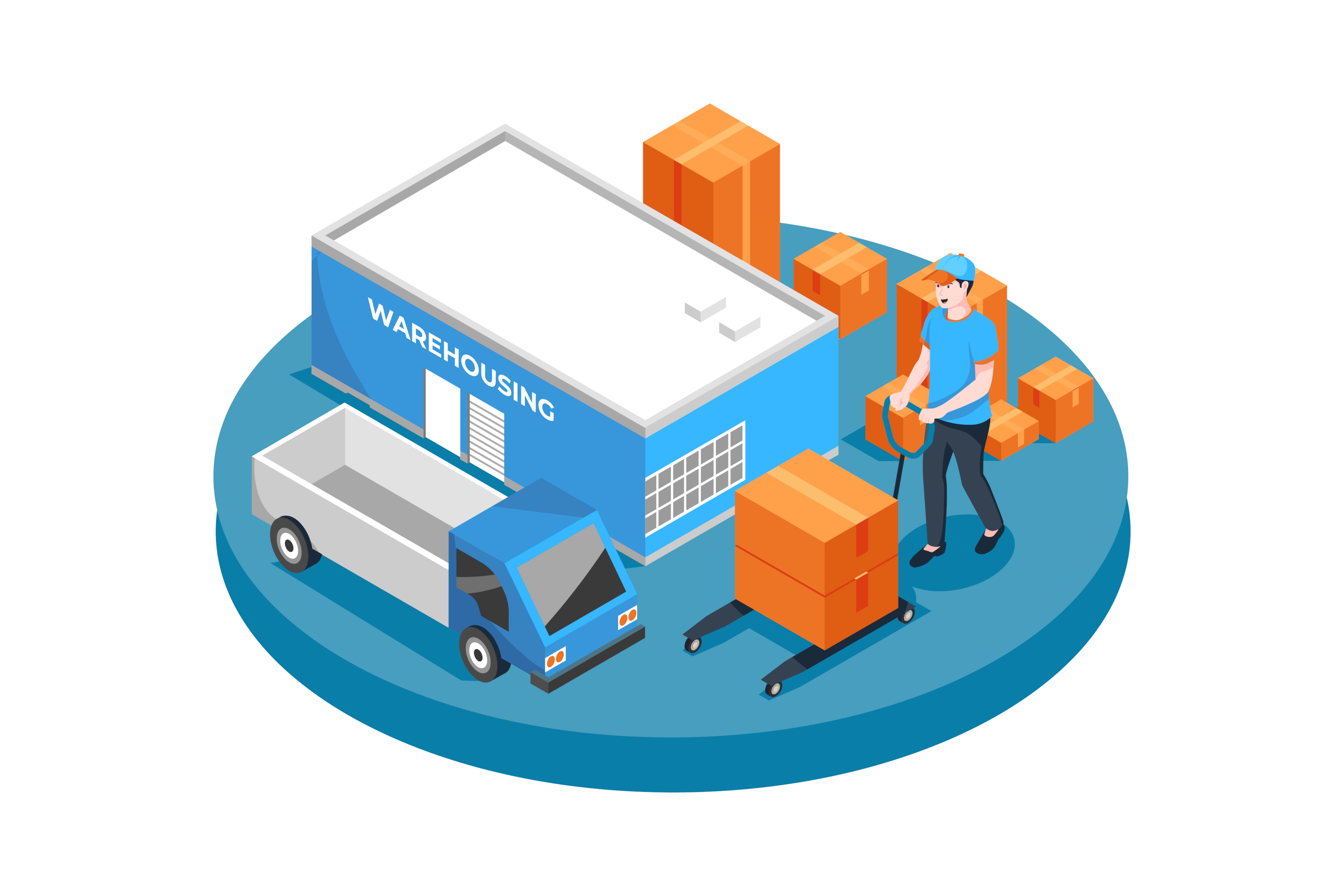
One thing is clear – a well-mapped warehouse A well-mapped warehouse saves time, money, and headaches. Clearly defined storage locations in warehouse mapping enhance inventory management, allowing easier tracking of items and better decision-making. Such organization is crucial for compliance and staying competitive in today’s market.
Effective mapping provides insights that optimize workflows and operational strategies. Identifying inefficiencies allows businesses to streamline workflows and enhance overall efficiency in warehouse facility operations. For example, a well-mapped warehouse layout can reduce travel time for staff, leading to faster order fulfillment and reduced labor costs.
Furthermore, warehouse mapping significantly contributes to operational efficiency. It allows for better warehouse space utilization depending on the types of warehouses, ensuring that every square foot of the warehouse is used effectively. This organized approach not only improves productivity but also enhances the overall efficiency of warehouse operations, making it a crucial component of effective warehouse management.
Key Elements of a Successful Warehouse Mapping System
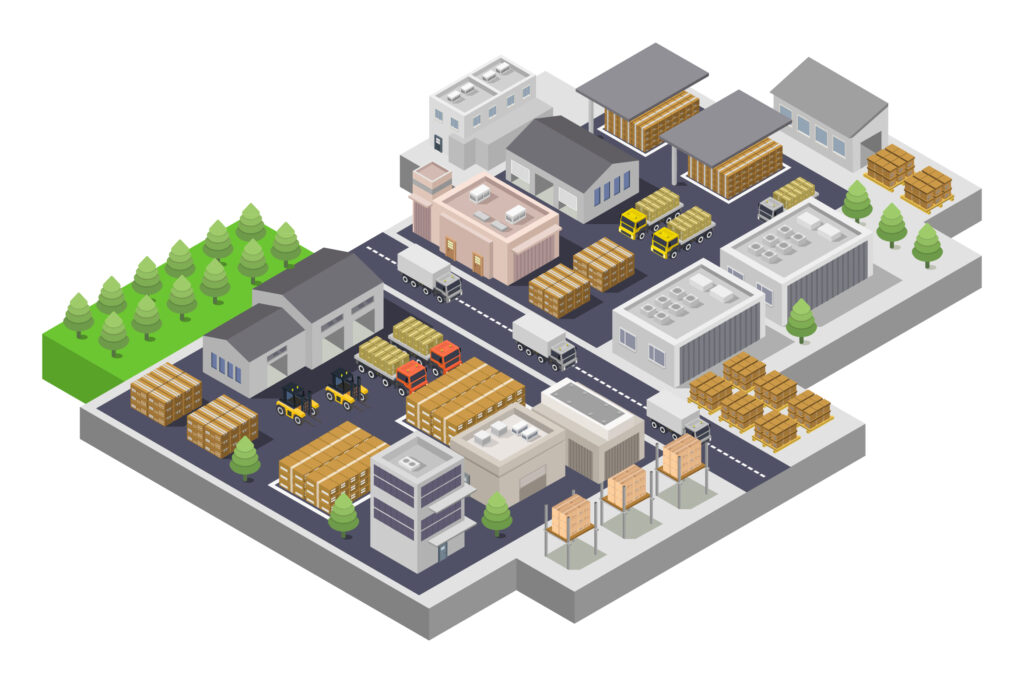
Implementing a structured mapping system is essential for organizing storage areas and improving item retrieval. By ensuring specific locations for each item, warehouse mapping can significantly enhance inventory accuracy and help in stock control. This systematic approach helps warehouse staff quickly locate items, reducing search times and increasing productivity.
A successful mapping system incorporates visual representations like reusable components and labeled areas to enhance usability. Logical numbering or naming systems for storage areas facilitate easy navigation for warehouse staff. Regular reviews and updates are necessary to maintain an effective mapping system, ensuring it adapts to changes in inventory and operational needs.
Interactive mapping software provides a dynamic view of inventory locations and assists in managing inventory thresholds. This allows for real-time inventory tracking and efficient inventory management. Feedback from warehouse associates is also crucial in creating an effective location mapping plan that reflects the realities of warehouse operations, including interactive maps.
11 Steps to Create an Efficient Warehouse Map
Creating an efficient warehouse map – essential for smooth first mile delivery – involves creating several key steps. Let’s consider them in more detail.
Step 1: Walk Through the Space
Start by walking the floor and observing how it’s used. Label zones with sticky notes or tape. Focus on high-traffic areas and bottlenecks.
Step 2: Review Current Layout
Evaluate how well your current layout supports picking strategies. Identify inefficiencies or overcrowded sections.
Step 3: Gather Staff Input
Talk to warehouse workers. They know what works – and what doesn’t – on the ground.
Step 4: Sketch the Initial Layout
Draft a basic map based on real use. Include docks, picking zones, packing areas, and storage.
Step 5: Assign Logical Labels
Give zones and aisles easy-to-read names. Use numbering that aligns with your WMS.
Step 6: Use Visual Cues
Incorporate signage, color-coding, and floor markers. Make navigation easy and intuitive.
Step 7: Integrate Technology
Connect your map to warehouse management tools. Real-time updates and tracking enhance accuracy.
Step 8: Test the Flow
Run mock workflows. Check for traffic jams, confusing labels, or unused zones.
Step 9: Train Staff
Introduce the map through onboarding and refresher training. Ensure everyone knows how to navigate and update zones.
Step 10: Reassess and Update Regularly
Schedule periodic reviews. Keep the map aligned with seasonal shifts, new SKUs, or process changes.
Careful planning and execution of these steps help businesses develop a mapping system that maximizes space utilization, improves inventory tracking, and creates boosts operational efficiency. The following subsections will delve deeper into each of the steps described above, providing practical tips and insights to help you create an efficient warehouse map.
Pre-Mapping Preparation
Before diving into the mapping process or automated warehouse picking systems, it’s essential to conduct a thorough walkthrough of the warehouse facility. This initial assessment helps warehouse managers understand the current layout and identify highly-trafficked and trouble areas. During this walkthrough, key areas should be label areas using a pen and sticky notes to ensure a clear visual representation of the space.
Focusing on highly-trafficked and trouble areas during the assessment is crucial for identifying potential issues, bottlenecks, and inefficiencies. Comparing shelves unit locations to the current picking strategy can provide insights into how the layout can be optimized to improve productivity. This pre-mapping preparation is a crucial step in the process, laying the foundation for a successful warehouse mapping.
Thorough assessment of the layout enables managers to make informed decisions and necessary adjustments for an efficient mapping system. Such a proactive approach ensures the mapping process is well-planned and aligned with the distribution center overall goals, providing a comprehensive view of operations.
Engaging Warehouse Staff
Staff members have valuable insights into operational workflows that might not be immediately obvious to managers. Their input can help identify operational challenges and ensure that the mapping system reflects the realities of daily warehouse operations.
Knowledgeable and well-trained staff maintain effective workflows and ensure the success of the mapping system. Their involvement not only leverages their expertise but also fosters ownership and collaboration. This collaborative approach can lead to actionable insights that improve the overall efficiency of the warehouse.
Warehouse mapping also facilitates quicker onboarding of new employees by providing a clear layout for navigation, including warehouse maps. This can reduce training time and minimize mistakes, ultimately leading to a safer work environment and more efficient warehouse operations. Engaging warehouse staff is a critical component of creating an effective mapping system.
Step 11: Designing the Warehouse Layout
This is the final step in creating an effective mapping system. A well-planned mapping strategy can lead to better utilization of warehouse space, identifying areas that are underused and optimizing the overall layout.
Warehouse managers should identify highly trafficked work areas and optimize the layout to ensure an uninterrupted flow of people and materials. Observing pickers’ route lengths, whether they double back, and the accessibility of popular SKUs can provide valuable insights into how the layout can be improved. Testing the floor plan with mock workflows can help identify potential issues related to traffic patterns before full implementation.
Designing a layout that facilitates efficient movement and storage enhances productivity and reduces operational costs. This strategic approach to layout design ensures that the mapping system supports the overall goals of the warehouse operations.
Leveraging Technology in Warehouse Mapping
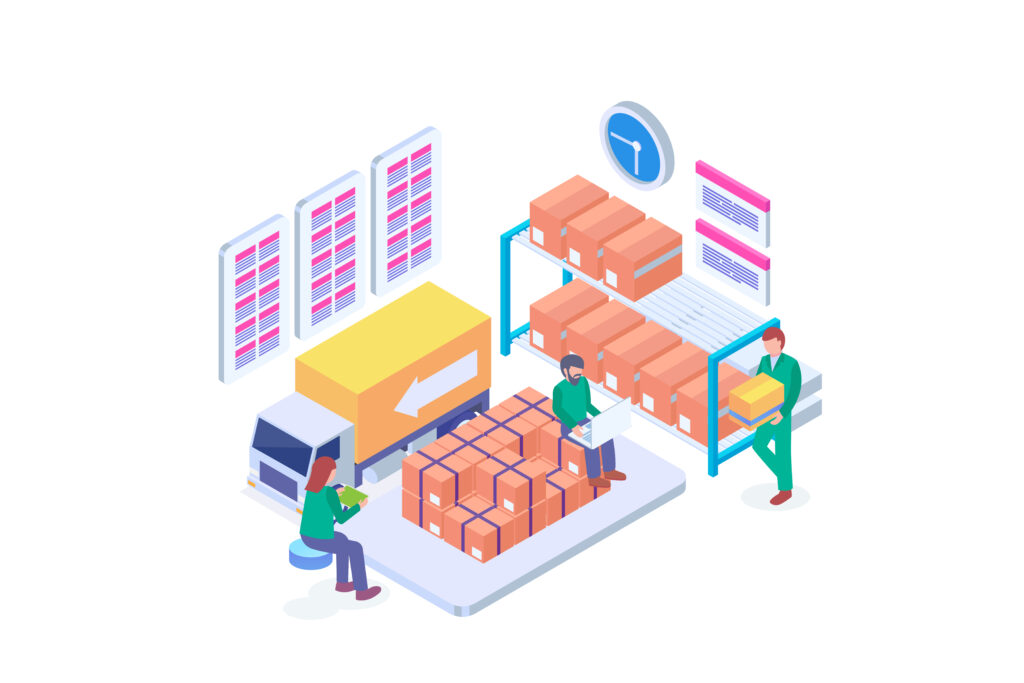
With help of technology, integrating mapping becomes even more effective. This way, the process can yield valuable insights into inventory movement and optimize travel time for warehouse staff by creating optimized paths for picking orders. Real-time inventory tracking reduces picking time and ensures quicker handoffs to your courier service partner.
Cloud-based warehouse management system allows for easier scalability and remote data access, providing better operational oversight. Data analytics tools in these software systems help businesses identify operational bottlenecks and optimize processes workflows.
IoT sensors and monitoring technologies not only ensure safety but also meet compliance standards tied to cargo insurance policies. Businesses that utilize real-time data and real time visibility can design efficient warehouse layouts. These layouts can effectively address both regulatory and operational requirements.
Addressing Common Warehouse Mapping Challenges
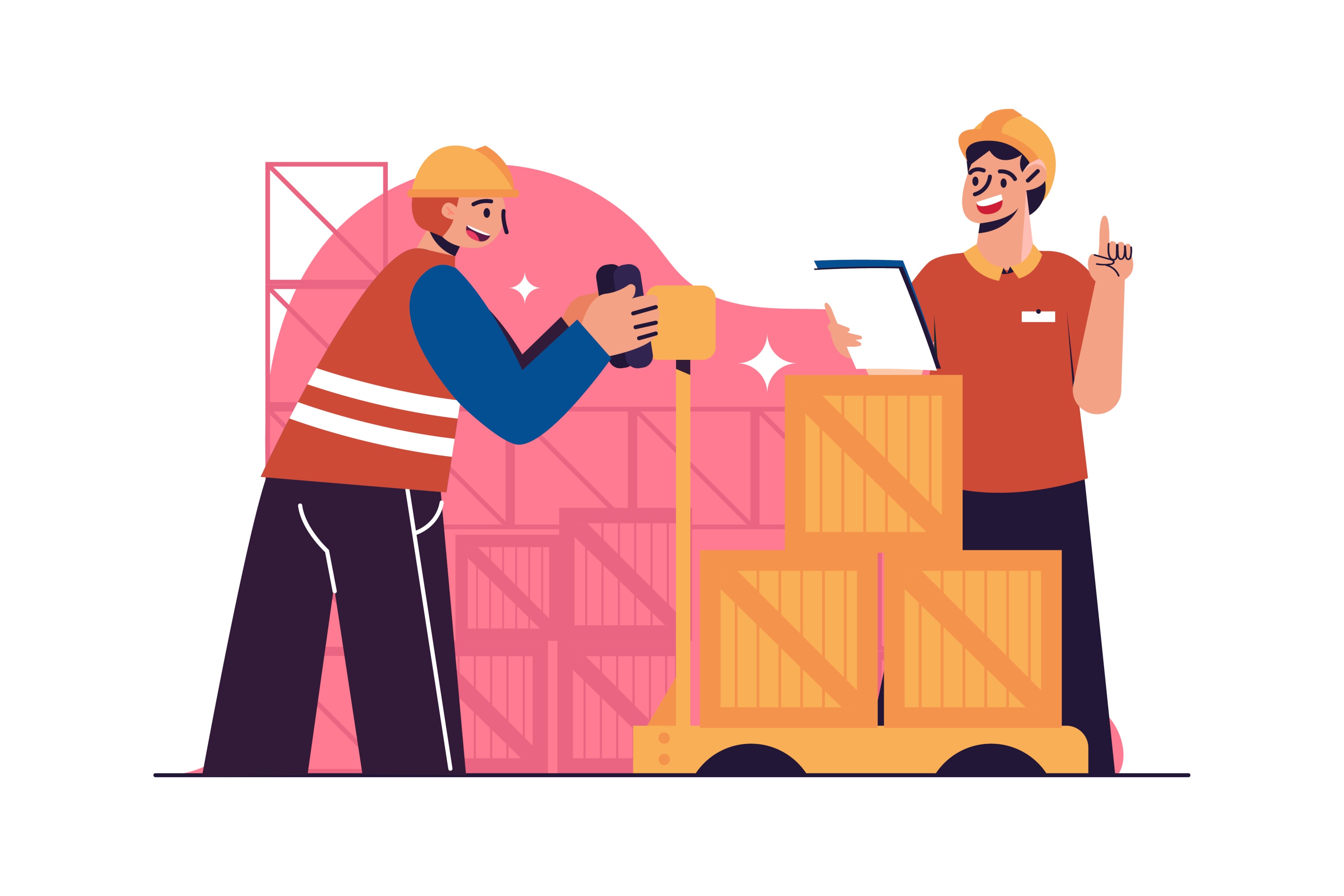
Despite the benefits of warehouse mapping, challenges can arise. Let’s look at a few of those.
1. Temperature Fluctuations
Temperature inconsistencies can severely impact product quality – especially when storing heat-sensitive or perishable goods. To address this, use thermal maps and IoT-enabled sensors to monitor climate conditions across different warehouse zones in real time. Based on this data, you can adjust your layout to ensure that temperature-sensitive items are stored in stable, controlled areas, reducing spoilage and ensuring compliance with storage regulations.
2. Outdated Layouts
Warehouse layouts that aren’t regularly reviewed can quickly become inefficient as inventory needs evolve. To prevent this, conduct quarterly mapping reviews to identify what’s working and what’s not. Encourage staff to report daily inefficiencies or bottlenecks they experience, as their insights can reveal issues that aren’t obvious from a management-level perspective. This proactive approach helps ensure your layout evolves alongside your operations.
3. Seasonal Inventory Changes
Fluctuations in stock due to seasonal demand can disrupt even the best-designed warehouse maps. Creating flexible storage zones that can be reconfigured quickly allows you to adapt to high-volume SKUs during peak periods. Rotating layouts seasonally ensures that your most in-demand items are always stored in accessible areas, keeping order fulfillment fast and efficient.
4. Lack of Internal Expertise
Not all teams have in-house experience with warehouse mapping, which can lead to inefficient DIY attempts. If your team lacks the necessary expertise, consider outsourcing the initial mapping design to professionals who specialize in layout optimization. Additionally, investing in user-friendly mapping software can guide your team through the process, offering templates and suggestions tailored to your warehouse type and inventory flow.
Proactively addressing these challenges ensures businesses maintain a great warehouse mapping system that supports efficient operations and meets regulatory requirements.
Regulatory Compliance in Warehouse Mapping
Regulatory compliance is a critical aspect of warehouse mapping. Guidelines from organizations like the United States Pharmacopeia (USP) should be followed to ensure proper warehouse mapping. Identifying hazardous areas, ensuring proper spacing, and maintaining clear egress paths are essential for compliance.
Qualification in warehouse mapping focuses on verifying that storage meets specified criteria. For pharmaceutical companies, following a comprehensive warehouse mapping procedure is crucial to ensure compliance. Regular evaluations and logging of data are vital to identify and address potential issues promptly.
Maintaining stable temperature conditions throughout the warehouse is essential for compliance. Products and equipment should be strategically placed to help achieve this stability – especially important for brands targeting temperature-sensitive segments like German market entry.
By following regulatory guidelines and maintaining a comprehensive mapping and warehouse management system, businesses can ensure regulatory compliance, SLA, and protect product integrity, especially for items that are stored.
Long-Term Benefits of Effective Warehouse Mapping
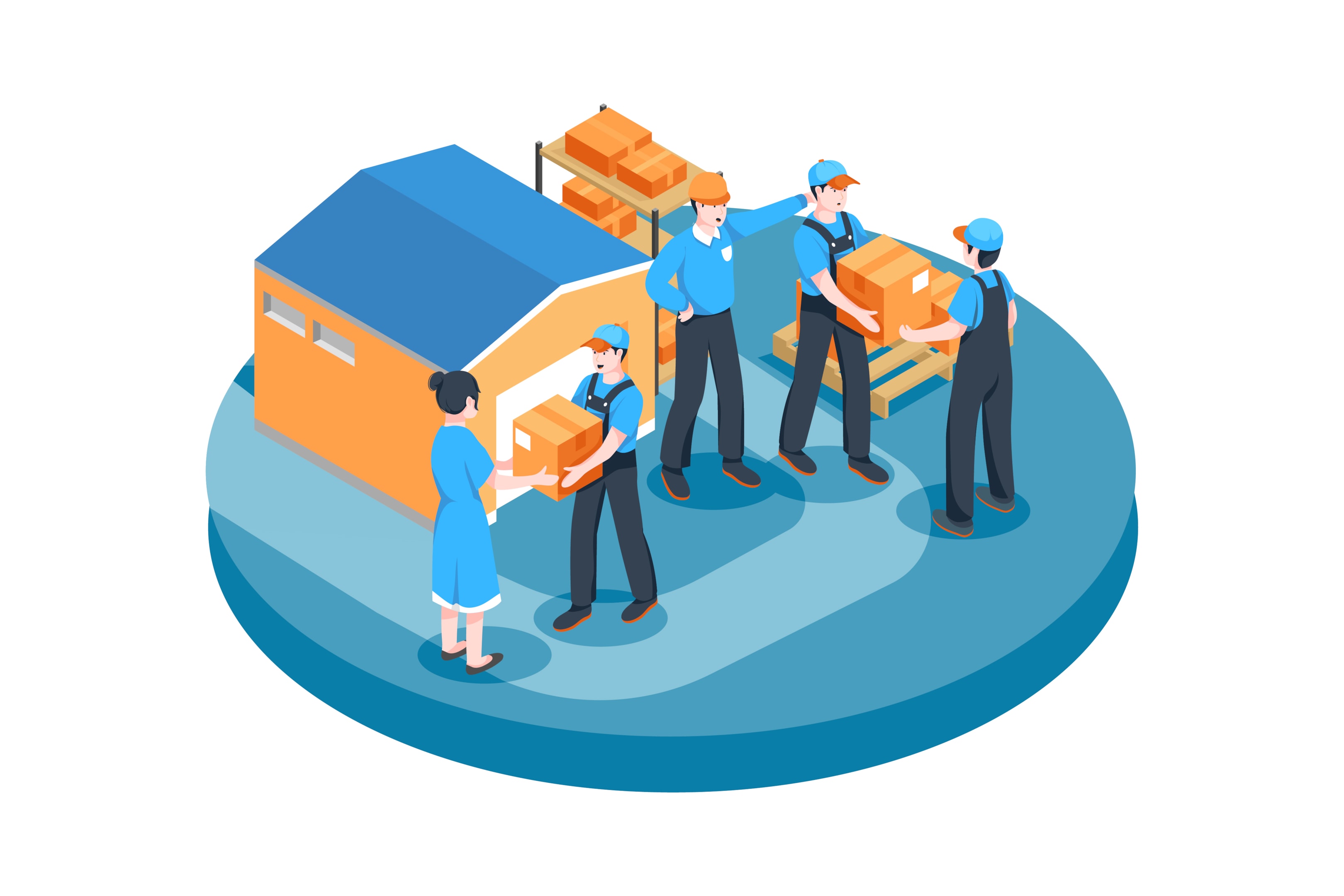
Effective warehouse mapping offers numerous long-term benefits. Here are some key advantages:
- Optimizes pick paths and minimizes search times, leading to significant savings in labor costs.
- Enhances operational efficiency.
- Helps identify previously underused spaces, leading to better allocation of storage areas.
By implementing warehouse mapping competently, businesses can improve their overall productivity and reduce costs.
Improved location identifiers allow warehouse personnel to quickly find and retrieve items, which boosts order fulfillment speed and overall productivity. A logical mapping system enables new employees to learn the warehouse layout faster, assigning specific locations, decreasing training time, and helping to save time while reducing mistakes.
These long-term benefits contribute to a more efficient and productive warehouse, ultimately supporting the overall business goals of the entire supply chain.
Summary
Warehouse mapping is a powerful tool for enhancing operational efficiency. By optimizing layouts, improving inventory tracking, and leveraging technology, businesses can achieve significant improvements in productivity and cost savings. Effective warehouse mapping also ensures regulatory compliance and supports the long-term goals of the warehouse operations.
Implementing these strategies can transform your warehouse into a well-organized and efficient hub, driving success across the entire supply chain. Embrace the power of warehouse mapping to unlock new levels of efficiency and productivity.
Frequently Asked Questions
Why is warehouse mapping important for operational efficiency?
Warehouse mapping is crucial for operational efficiency as it optimizes layouts and enhances inventory management, ultimately identifying inefficiencies. This leads to streamlined processes and improved overall productivity.
What are the key elements of a successful warehouse mapping system?
A successful system incorporates structured organization, visual representation, logical numbering systems, and regular updates to ensure efficiency and ease of navigation. Prioritizing these elements will lead to optimal warehouse management.
How can technology enhance warehouse mapping?
Technology significantly enhances the mapping process by utilizing systems like WMS and real-time inventory tracking, which optimize travel time and improve stock accuracy. This leads to increased efficiency and better resource management within the warehouse.
What are common challenges in warehouse mapping?
Common challenges in warehouse mapping include temperature inconsistencies, layout inefficiencies, and the necessity for regular updates. Addressing these issues is crucial for optimal warehouse operations.
How does warehouse mapping ensure regulatory compliance?
It ensures regulatory compliance by adhering to established guidelines, maintaining proper spacing and egress paths, and conducting regular evaluations and data logging. This structured approach minimizes risks and fosters a safer environment.